The Ultimate Guide to Acrylic Plastic
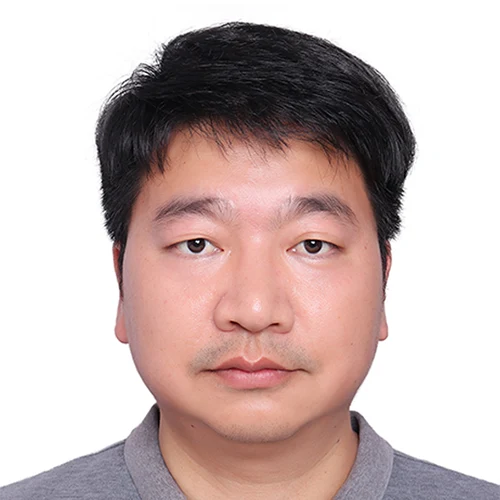
Founder of UKPACK, Chief Packaging Designer with 18 years of experience, Red Dot Award Winner
Specialize in custom, innovative, and sustainable packaging solutions for cosmetics, skincare, personal care, hair care, food and beverage, and more.
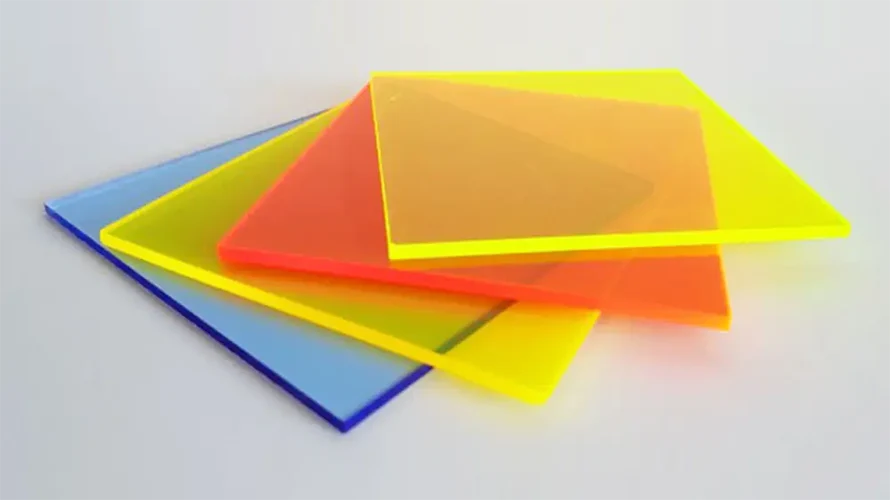
Acrylic plastic is a versatile material that has become a staple in many industries due to its unique properties. From cosmetics packaging to automotive parts, this material has found its way into a wide range of products and applications.
But with its growing popularity, it’s important to consider the environmental impact of acrylic plastic.
In this blog, we’ll explore the properties and uses of acrylic, examine its impact on the environment, and consider the future outlook for this material.
Whether you’re a manufacturer, consumer, or simply someone interested in sustainability, this is a topic you won’t want to miss.
So read on to learn more about acrylic plastic and its role in our world.
What is Acrylic Plastic?
Definition of acrylic plastic
Acrylic plastic, also known as polymethyl methacrylate (PMMA), is a synthetic thermoplastic polymer made from the polymerization of methyl methacrylate monomers. It is often referred to as plexiglass, which is a trademarked term for a specific brand of acrylic plastic.
Brief history of acrylic plastic
The history of acrylic plastic can be traced back to the 1930s. In 1933, German chemist Otto Rohm developed a process for synthesizing methyl methacrylate monomers, which would later become the building blocks for acrylic plastic.
In the decades that followed, acrylic plastic was developed into a versatile and widely used material, with its first commercial use as a replacement for glass in aircraft canopies during World War II. After the war, acrylic plastic continued to gain popularity, with uses ranging from construction and automotive to medical and consumer products.
Today, acrylic plastic is one of the most widely used thermoplastic materials in the world, and its unique combination of transparency, toughness, and weather resistance makes it a popular choice for a wide range of applications. Despite its many advantages, it is important to consider the environmental impact of using this material when selecting it for a specific application.
Characteristics and properties of acrylic plastic
The characteristics and properties of acrylic plastic are as follows:
- Transparency: Acrylic has high optical clarity, making it a popular choice for applications that require transparency, such as windows, lenses, and displays.
- Lightweight: PMMA is lighter than glass, making it easier to handle and transport.
- Durability: It is strong, resistant to impact and weathering, and has good dimensional stability.
- Chemical resistance: It is resistant to many chemicals, including acids and alkalis.
- UV resistance: Acrylic has excellent resistance to UV radiation, making it ideal for outdoor applications.
- Easy to fabricate: Acrylic is easy to fabricate, cut, drill, bend, and glue, making it a popular choice for a wide range of applications.
- Good electrical insulation: It is a good electrical insulator, making it suitable for electrical applications.
- Low flammability: Acrylic has low flammability and a high ignition point, making it a safer alternative to some other materials.
- Eco-friendly: Plexiglass is a recyclable material, and its production generates less waste and greenhouse gas emissions than some other materials.
Types of Acrylic Plastic
Extruded acrylic
Extruded acrylic is a type of acrylic plastic produced by a continuous process where the raw material is melted and formed into a sheet. In this process, the raw material is melted and forced through a die to form a continuous sheet. The sheet is then cooled and cut to size.
By the eay, ectruded acrylic is the least expensive type of acrylic and is often used for lower quality applications. It has lower optical clarity compared to cast acrylic and may have visible flow lines and surface defects. Despite these limitations, extruded acrylic is still a versatile material with good strength, durability, and resistance to weathering and impact.
Cast acrylic
Cast acrylic, also known as cast polymethyl methacrylate (PMMA), is a type of acrylic plastic produced by pouring the raw material into a mold and allowing it to cool and cure. The mold is carefully designed to ensure an even distribution of the material and to prevent the formation of air bubbles.
Moreover, cast acrylic has a higher quality and clarity compared to extruded acrylic, and it is often used for applications that require high optical clarity and surface quality, such as windows, lenses, and displays.
what’s more, cast acrylic has good resistance to impact, weathering, and chemicals, and it has a smooth surface finish that can be easily polished.
Additionally, cast acrylic has excellent dimensional stability and can be easily fabricated into a variety of shapes and sizes.
Cell-cast acrylic
Cell-cast acrylic is a type of cast acrylic that is made using a special mold that produces a cell structure within the material. This cell structure gives cell-cast acrylic improved strength and stiffness compared to standard cast acrylic. It also makes the material more resistant to impact and better suited for applications where the material is subject to stress.
The production process for cell-cast acrylic is similar to standard cast acrylic, but the special mold allows for the formation of the cell structure during the curing process. This results in a material with improved properties and a higher quality compared to extruded acrylic.
Cell-cast acrylic is often used for high-end applications, such as skylights, displays, and other applications that require high optical clarity and strength.
Impact-modified acrylic
Impact-modified acrylic is a type of acrylic plastic that is made by adding a small amount of an impact modifier to the raw material before it is processed. The impact modifier helps to improve the material’s resistance to impact and to make it more flexible. This results in a material that is more resistant to breakage and more suitable for applications where the material is subject to stress.
The production process for impact-modified acrylic is similar to standard cast acrylic or extruded acrylic, but with the addition of the impact modifier. Impact-modified acrylic is often used for applications that require a high level of impact resistance, such as signs, displays, and protective covers.
Additionally, it is also used in applications that require a combination of good optical clarity and impact resistance, such as skylights and windows.
Manufacturing Process of Acrylic Plastic
Steps involved in the production of acrylic plastic
The manufacturing process of acrylic plastic involves the following steps:
- Raw material preparation: The raw material, which is usually a combination of methyl methacrylate (MMA) monomers and a polymerization initiator, is carefully weighed and prepared according to the manufacturer’s specifications.
- Polymerization: The prepared raw material is placed in a reactor, where it is subjected to heat and pressure. The polymerization initiator causes the monomers to react and form long chains of polymer, which is the basic building block of the acrylic plastic.
- Extrusion or casting: Depending on the desired type of acrylic plastic, the polymer is either melted and forced through a die to form a continuous sheet (extrusion), or it is poured into a mold and allowed to cool and cure (casting).
- Fabrication: The resulting acrylic plastic is then cut to size and fabricated into the desired shape and form using techniques such as sawing, drilling, milling, and polishing.
The manufacturing process produces a material with good optical clarity, resistance to impact, weathering, and chemicals, and excellent dimensional stability.
Different types of acrylic plastic, such as extruded, cast, cell-cast, or impact-modified, can be produced by modifying the manufacturing process and the raw materials used.
Techniques used in the fabrication of acrylic plastic
There are several techniques used in the fabrication of acrylic plastic, including:
- Sawing: Acrylic plastic can be cut to size using a saw, such as a band saw or circular saw. The saw blade must be carefully selected to ensure a clean and accurate cut without cracking or melting the material.
- Drilling: Holes can be drilled into acrylic plastic using a drill press or a hand drill. Specialized bits are used to prevent cracking and melting of the material.
- Milling: Complex shapes can be produced by milling the acrylic plastic using a CNC router or a milling machine. The tool path is carefully designed to ensure accurate and efficient production of the desired shape.
- Polishing: The surface of the acrylic plastic can be polished to improve its optical clarity and to remove any surface defects. This is done using abrasive polishing compounds and a buffing wheel.
Advantages and Disadvantages of Acrylic Plastic
- Optical Clarity: It has excellent optical clarity, making it ideal for applications such as windows, displays, and lighting fixtures.
- Weather Resistance: It is highly resistant to weathering, making it ideal for outdoor applications such as signs and protective covers.
- Impact Resistance: It has good impact resistance, making it ideal for applications such as protective covers and safety shields.
- Chemical Resistance: It is resistant to many chemicals, including many acids, alkalis, and solvents, making it ideal for applications such as laboratory equipment and chemical storage containers.
- Lightweight: Acrylic plastic is lightweight, making it easy to handle and ideal for applications such as displays and signage.
- Dimensional Stability: Plexiglass has excellent dimensional stability, which means that it does not warp or deform over time, making it ideal for applications that require precise dimensions.
Disadvantages of acrylic plastic:
- Scratches Easily: It is easily scratched, which can affect its optical clarity and overall appearance.
- UV Light sensitivity: It is sensitive to UV light, which can cause yellowing and degradation over time.
- Flammability: It is flammable and can emit toxic fumes when burned, making it less suitable for applications in high-heat environments.
- Higher Cost: It is typically more expensive than other types of plastic, which can make it less suitable for large scale or cost-sensitive applications.
- Limited color availability: It is available in limited colors, which can limit its versatility and flexibility for certain applications.
Applications of Acrylic Plastic
- Cosmetic packaging: PMMA is widely used in the cosmetic packaging industry due to its transparency, light weight, and ability to be molded into different shapes. This makes it ideal for packaging cosmetic products such as lotions, creams, and perfumes. UKPACK is a professional cosmetic packaging manufacturer in China, we can offer acrylic cosmetic packaging such as acrylic cosmetic bottles, and acrylic cosmetic jars in a wide range of styles and designs.
- Construction industry: PMMA is commonly used in the construction industry due to its durability, weather resistance, and ability to be molded into different shapes. It is used in windows, skylights, and as a substitute for glass.
- Automotive industry: Plexiglass is used in the automotive industry for the manufacture of windshields, rear windows, and sunroofs. Its lightweight and weather resistance make it an ideal choice for these applications.
- Medical and scientific equipment: Acrylic plastic is used in the medical and scientific fields due to its transparency, ease of sterilization, and ability to be molded into complex shapes. This makes it ideal for use in laboratory equipment, medical devices, and even as protective covers for electronic equipment.
- Consumer products and electronics: Plexiglass is commonly used in the production of consumer products and electronics due to its transparency, light weight, and ease of molding. It is used in the manufacture of products such as cell phone cases, computer screens, and even toys.
- Bathroom Products: Acrylic is a lightweight, durable, and aesthetically pleasing material widely used in bathroom products. Acrylic bathtubs are a prime example, offering a warm touch, excellent heat retention, and versatile designs to suit various home styles. Additionally, acrylic is commonly used in washbasins, shower panels, and more, thanks to its smooth surface, easy maintenance, and resistance to chemical corrosion. Combining functionality with elegance, acrylic bathroom products provide a high-quality choice for modern bathroom spaces.
Environmental Impact of Acrylic Plastic
- Recycling of acrylic plastic: Although acrylic plastic can be recycled, the process is not widely available and the majority of acrylic plastic ends up in landfills or the ocean. In these environments, the plastic can take hundreds of years to break down, leading to long-term environmental damage.
- Energy consumption and greenhouse gas emissions during production: The production of acrylic plastic requires large amounts of energy and releases significant amounts of greenhouse gases into the atmosphere. These emissions contribute to global warming and climate change.
- Impact on wildlife and marine life: Acrylic plastic can have a significant impact on wildlife and marine life. When plastic debris enters the ocean, it can entangle and kill marine animals such as sea turtles, dolphins, and whales. Ingestion of plastic debris by marine animals can also lead to the release of toxic chemicals into the food chain. Plastic debris can also cause physical harm to birds and other land-based wildlife.
Overall, the environmental impact of acrylic plastic highlights the importance of reducing plastic consumption and increasing recycling efforts to protect the planet.
Conclusion
Acrylic plastic is a versatile material with a range of properties that make it suitable for use in a variety of applications. These properties include transparency, light weight, and ability to be molded into different shapes. Acrylic plastic is commonly used in the cosmetic, construction, automotive, medical and scientific, and consumer product industries.
However, despite its widespread use, acrylic plastic also has a significant impact on the environment. This impact can be seen in the energy consumption and greenhouse gas emissions during production, as well as the lack of widespread recycling and the harm it can cause to wildlife and marine life.
The future outlook for acrylic plastic remains uncertain, with ongoing efforts to reduce plastic consumption and increase recycling efforts. It is important to consider the environmental impact of this material and to seek out alternative, sustainable materials where possible.
UKPACK is on a mission to offer sustainable cosmetic packaging to all cosmetics, beauty, and skincare brands.