The Ultimate Guide to HDPE Plastic
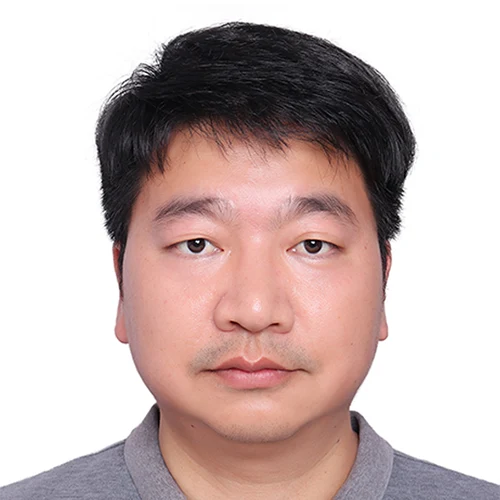
Founder of UKPACK, Chief Packaging Designer with 18 years of experience, Red Dot Award Winner
Specialize in custom, innovative, and sustainable packaging solutions for cosmetics, skincare, personal care, hair care, food and beverage, and more.
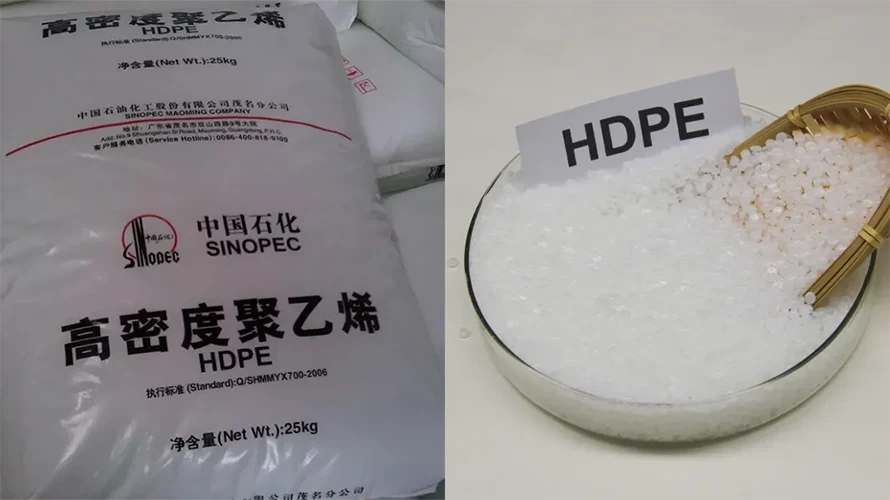
What is HDPE Plastic?
First of all, HDPE stands for High Density Polyethylene. It’s a plastic made from petroleum, and it’s very sturdy and durable. You can use it for many things because it doesn’t absorb water, so you can use it in damp places.
You can make a lot of things with HDPE plastic, like packaging, containers for holding things, household items, medical equipment, building materials, and even membranes to prevent seepage.
Finally, many people like to use HDPE plastic because it’s easy to recycle, so it doesn’t have much impact on the environment.
What are the Properties of HDPE
HDPE (High Density Polyethylene) plastic has a number of unique properties that make it a popular choice for various applications:
High strength-to-density ratio
The high strength-to-density ratio of HDPE plastic is one of its most notable properties. The density of HDPE ranges from 930 to 970 kg/m3. Despite having a slightly higher density than low-density polyethylene (LDPE), HDPE has a higher tensile strength (38 MPa versus 21 MPa) due to its lack of branching, which gives it stronger intermolecular forces. This means that HDPE can withstand greater stress and pressure compared to LDPE, while still maintaining its lightweight nature.
The lack of branching in HDPE is achieved through the use of a specific catalyst, such as Ziegler-Natta catalysts, and appropriate reaction conditions. This results in a strong and durable plastic that is ideal for use in applications that require high strength and low weight, such as pipes and containers.
Chemical resistance
HDPE plastic is well known for its chemical resistance, which makes it an ideal choice for applications where exposure to harsh chemicals is a concern. This property of HDPE is due to its strong and tightly packed molecular structure, which makes it difficult for chemicals to penetrate and react with the plastic.
HDPE has a high resistance to many organic and inorganic chemicals, including strong acids and bases, alcohols, and salt solutions. This makes it an ideal choice for applications such as chemical storage containers, chemical transfer pipes, and chemical processing equipment. It is also commonly used in the food and beverage industry for applications such as food packaging and containers, as it is safe for contact with food and is resistant to many food-based chemicals.
Weather resistance
HDPE has excellent weather resistance, making it a popular choice for outdoor applications. This material has the ability to maintain its properties even when exposed to the elements, including extreme temperatures, sunlight, rain, and wind.
One of the key factors contributing to HDPE’s weather resistance is its ability to resist UV radiation. HDPE has a natural resistance to UV rays, which can cause degradation and discoloration in other types of plastic. As a result, HDPE products can maintain their original color and strength for many years, even when exposed to direct sunlight.
Another factor contributing to HDPE’s weather resistance is its stability in extreme temperatures. HDPE can withstand temperatures ranging from -50°C to 80°C, making it suitable for use in a wide range of outdoor applications. The material does not become brittle or crack in cold temperatures, and it does not deform or soften in high temperatures.
Moreover, HDPE also has good resistance to moisture, making it ideal for applications that are exposed to rain and other forms of precipitation. The material is not affected by water absorption, and it does not become weaker or more brittle over time when exposed to moisture.
Overall, HDPE’s weather resistance makes it a popular choice for outdoor applications, including water pipes, drainage systems, playground equipment, and more. To ensure that HDPE products continue to perform well in the long term, it’s important to consider the specific requirements of the application and to choose a high-quality HDPE material that meets these requirements.
Impact resistance
HDPE also has exceptional impact resistance, which makes it a popular choice for a wide range of applications, including packaging, toys, sports equipment, and industrial parts.
One of the key factors contributing to HDPE’s impact resistance is its high molecular weight. The high molecular weight of HDPE gives it greater strength and rigidity compared to other plastics, allowing it to absorb more energy before cracking or breaking.
Another factor contributing to HDPE’s impact resistance is its low brittleness temperature. Unlike other plastics that become brittle and prone to cracking in cold temperatures, HDPE maintains its flexibility even in low temperatures, making it suitable for use in harsh weather conditions.
Moreover, HDPE also has good ductility, which allows it to deform without breaking when subjected to stress. This property allows HDPE to absorb impacts without cracking or breaking, making it ideal for applications that require high impact resistance.
Fatigue resistance
Fatigue resistance is an important property of materials that are subject to repeated stress and loading over time. HDPE has excellent fatigue resistance, making it a popular choice for a wide range of applications that require repeated loading and unloading.
The high molecular weight of HDPE gives it greater strength and rigidity compared to other plastics, which enhances its fatigue resistance. This high molecular weight also allows HDPE to absorb more energy before cracking or breaking, which is essential for materials that are subject to repeated stress and loading.
HDPE’s molecular structure also contributes to its fatigue resistance. Unlike other plastics that have a linear molecular structure, HDPE has a branched molecular structure that enhances its ability to absorb stress and energy. This branched molecular structure gives HDPE a higher tensile strength and modulus of elasticity, making it more resistant to fatigue and deformation over time.
Food grade
HDPE is an FDA (Food and Drug Administration) approved food contact material and is commonly used for packaging food and beverage products. To ensure that HDPE products are safe and suitable for food and beverage applications, it’s important to choose a high-quality HDPE material that is specifically designed for food-grade applications and meets all relevant regulatory requirements.
Manufacturing and Production of HDPE
Raw materials used in HDPE production
Ethylene is the main raw material used in the production of HDPE, it is a colorless and flammable gas that is derived from petroleum. Other raw materials used in the production of HDPE include:
- Alpha-olefins: Alpha-olefins are used to control the molecular weight of the polymer and to improve its physical properties, such as tensile strength, impact resistance, and stiffness.
- Catalysts: Catalysts are used to initiate the polymerization of ethylene and to control the properties of the final HDPE product. Common catalysts used in the production of HDPE include Ziegler-Natta catalysts, metallocene catalysts, and chromium-based catalysts.
- Inhibitors: Inhibitors are used to control the polymerization reaction and to prevent the formation of unwanted by-products.
- Modifiers: Modifiers are used to improve the physical properties of HDPE, such as its toughness, flexibility, and chemical resistance. Common modifiers used in HDPE production include butene, hexene, and octene.
- Antioxidants: Antioxidants are used to protect HDPE from thermal oxidation and to extend its useful life.
Process Steps of HDPE production
The production of HDPE plastic involves several processing steps:
- Raw Material Preparation: The first step in HDPE production is to prepare the raw materials. This includes the sourcing of high-density polyethylene monomers, such as ethylene, and any necessary co-monomers.
- Polymerization: The next step is polymerization, which is the process of combining the monomers to form long chains of polymer molecules. This can be done using various methods, including low-pressure polymerization and high-pressure polymerization. The high-pressure method is commonly used in the production of HDPE, as it results in a higher-quality product with fewer impurities.
- Pelletization: After polymerization, the polymer is melted and formed into small pellets. These pellets can then be stored or transported for further processing.
- Molding: The next step in HDPE production is molding, which is the process of shaping the polymer into its final form. There are various molding methods that can be used, including injection molding, blow molding, and extrusion molding. The specific method used will depend on the intended end use of the HDPE product.
- Cooling and Cutting: After molding, the product is cooled and cut into the desired shape and size.
- Testing and Quality Control: The final step in HDPE production is testing and quality control. This involves checking the physical and mechanical properties of the product to ensure that it meets the desired specifications and industry standards.
What is HDPE Plastic Used for?
HDPE (High-Density Polyethylene) plastic is widely used in many different applications due to its unique combination of properties.
Packaging
Some of the common packaging applications of HDPE include:
- Milk and juice containers: HDPE containers are used to package liquids such as milk, juice, and other dairy products. They are lightweight, leak-proof, and offer protection from contamination.
- Plastic bags: HDPE is used to make lightweight, strong, and flexible plastic bags for shopping, grocery, and other purposes.
- Plastic bottles: HDPE bottles are commonly used to package a wide range of products, including household cleaners, personal care items, and food products.
- Food packaging: HDPE is used to make food packaging containers and trays that are safe for food contact and preserve the freshness of the food.
- Cosmetic packaging: They are used for lotion bottles, foam pump bottles, tubes, jars, caps and closures, and more.
- Pharmaceutical packaging: HDPE is used to make containers and bottles for pharmaceuticals, including over-the-counter medicines, prescription drugs, and vitamins.
- Industrial packaging: HDPE is used in the packaging of industrial products such as chemicals, lubricants, and automotive products.
HDPE Plastic Recycling Processes
HDPE plastic recycling is an important process that helps to reduce waste, conserve resources, and reduce the impact of plastic waste on the environment. The recycling of it involves several steps, which are as follows:
- Collection: HDPE plastic waste is collected from various sources such as households, industrial units, and commercial establishments. The collected waste is sorted into different categories of plastic materials, such as HDPE, LDPE, PET, and others.
- Sorting: The collected HDPE plastic waste is then sorted based on the type, color, and quality of the material. This step is essential to ensure that the recycled plastic is of high quality and suitable for further processing.
- Shredding: The sorted HDPE plastic is then shredded into small pieces using specialized machines. This helps to reduce the size of the plastic and make it easier to transport and store.
- Washing: The shredded HDPE plastic is then washed to remove any impurities, such as dirt, oil, and other contaminants. The washing process also helps to increase the quality of the recycled plastic.
- Drying: After washing, the shredded HDPE plastic is then dried to remove any remaining moisture. This step is important to ensure that the recycled plastic is free of moisture, which can affect the quality of the final product.
- Melting: The dried shredded HDPE plastic is then melted using specialized machines. The melted plastic is then passed through a filter to remove any remaining impurities.
- Pelletizing: The filtered melted HDPE plastic is then passed through a pelletizing machine, which forms it into small pellets. These pellets are then cooled and packaged for further use.
- End Use: The recycled HDPE plastic pellets can be used to produce a wide range of products, including containers, pipes, packaging materials, and more.
Conclusion
HDPE plastic is a versatile and durable material with numerous applications, it’s also BPA-free. With the increasing concern for the environment, HDPE’s recyclable nature is also likely to drive its demand. Governments and organizations around the world are promoting the use of environmentally-friendly products, and HDPE is likely to play a crucial role in meeting these goals.